Product Details
Product name | AR FIBERGLASS CHOPPED STRANDS | ||
MOQ | ≥1000KG | ||
Zro2 Content | 14.5% & 16.5% | ||
Application | 1. Mortar and concrete reinforcement (GFRC). 2. Fireplace surrounds. 3. All decorative applications as countertops. | ||
Feature | 1. Strengthen the concrete and helps prevent cracking from shrinkage. 2. Replace steel reinforcement in countertops. 3. Suitable for use with any concrete countertop project. |
PERFORMANCE ATTRIBUTES
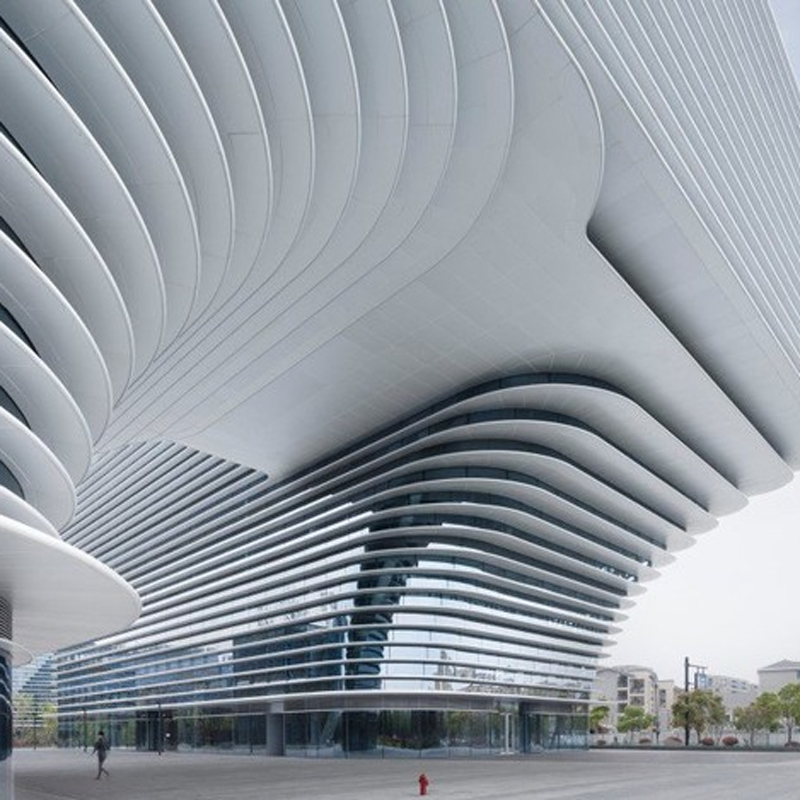
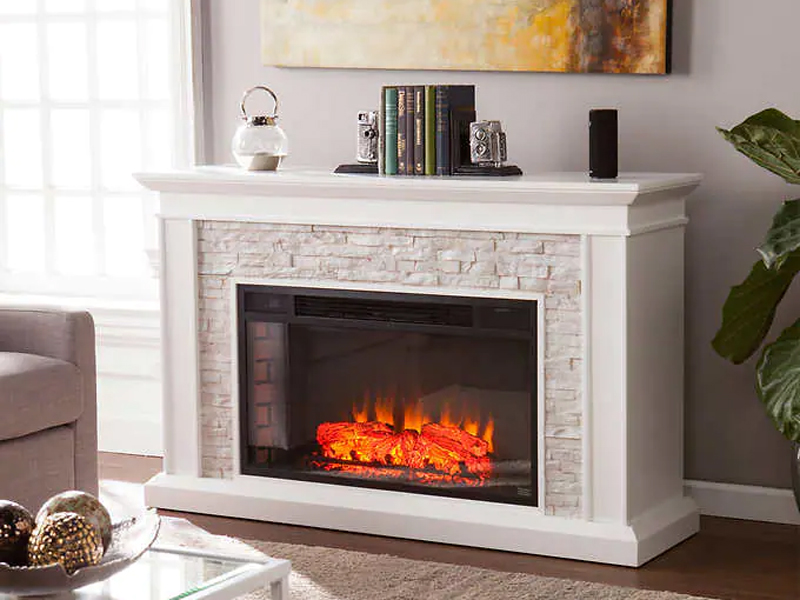
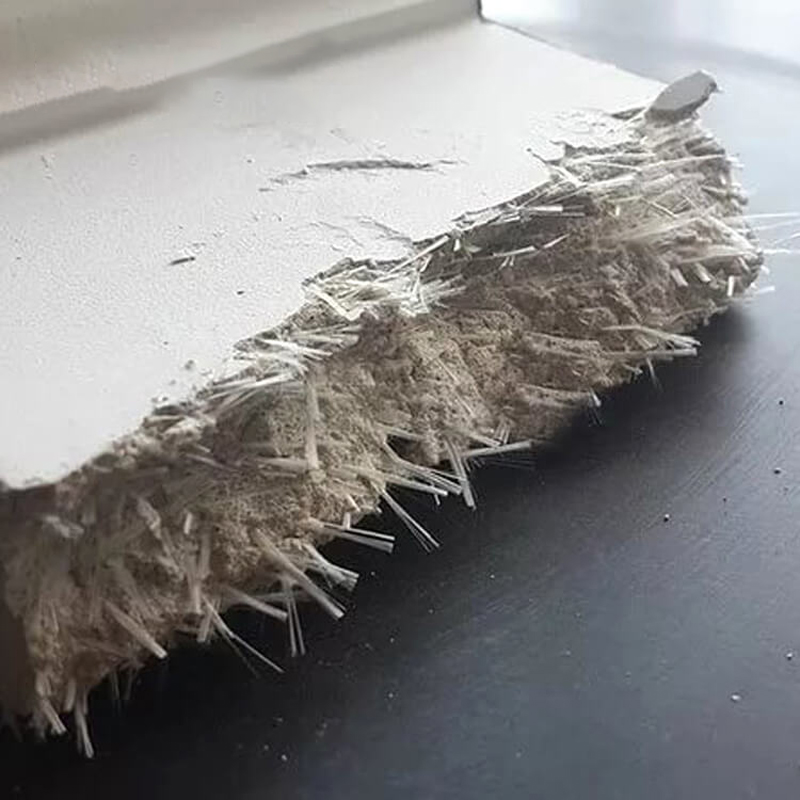
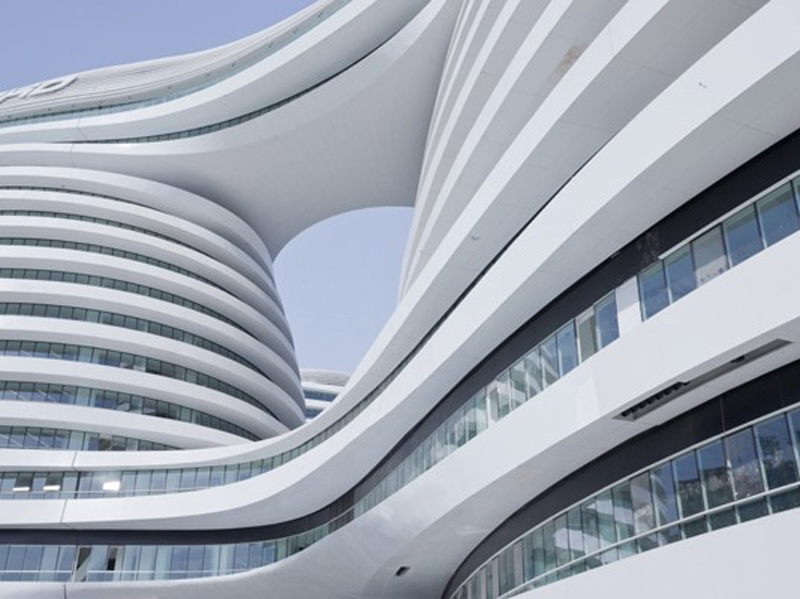
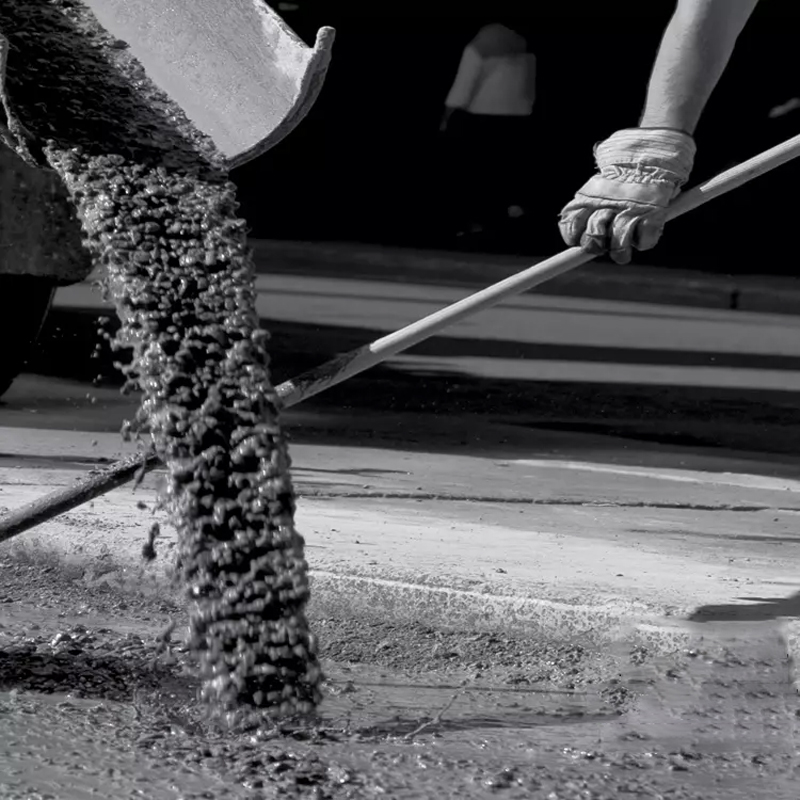
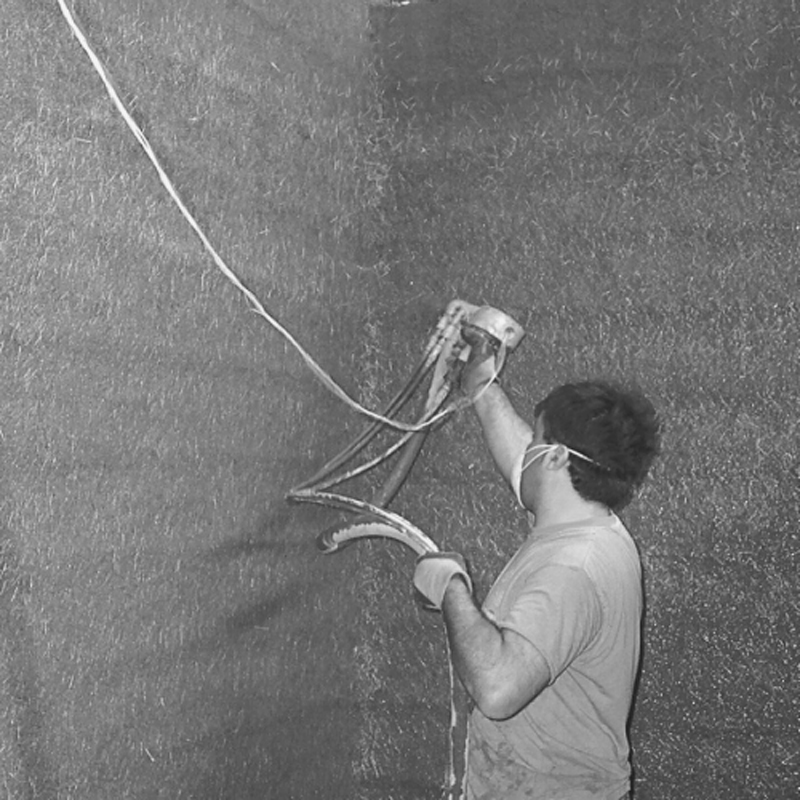
MAKES HIGHLY DURABLE GRC ELEMENTS
REMAINS INTEGRAL DURING MIXING
SUITABLE FOR BOTH PREMIX AND SPRAY
REINFORCED CONCRETE AS A STRUCTURAL MATERIAL
Technical Index
Yarn Density per Strand(tex) | Content of Fuel(%) | Moisture Content(%) | Length(mm) |
98±10 | 1.6±0.2 | ≤0.2 | 6、12、18、24 |
58±10 | 1.6±0.2 | ≤0.2 | 6、12、18、24 |
Specification
Product Code | Unit | ARGCTM12 | ARGCTM18 | ARGCTM24 |
Fiber Diameter | Microns | 13±2 | 13±2 | 13±2 |
Chop Length) | mm | 12 | 18 | 24 |
Linear Density | tex | 76±7 | 76±7 | 76±7 |
ZrO2 Content | % | ≥16 | ≥16 | ≥16 |
Moisture Content | % | ≤0.2 | ≤0.2 | ≤0.2 |
Breaking Strength | N/tex | ≥0.25 | ≥0.25 | ≥0.25 |
APPLICATION
It used in the manufacture of glass fiber reinforced concrete (GRC) composites by both premix and simultaneous spray methods; fireplace surrounds; all decorative applications as countertops.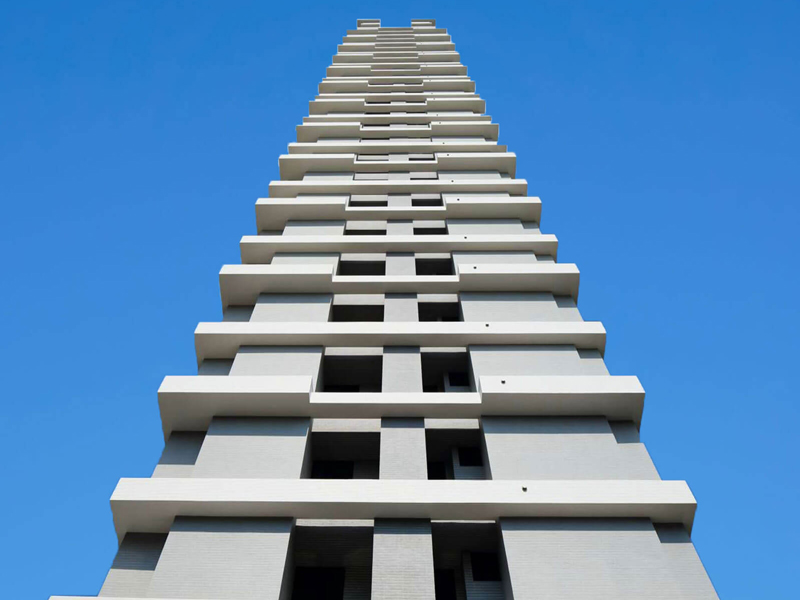
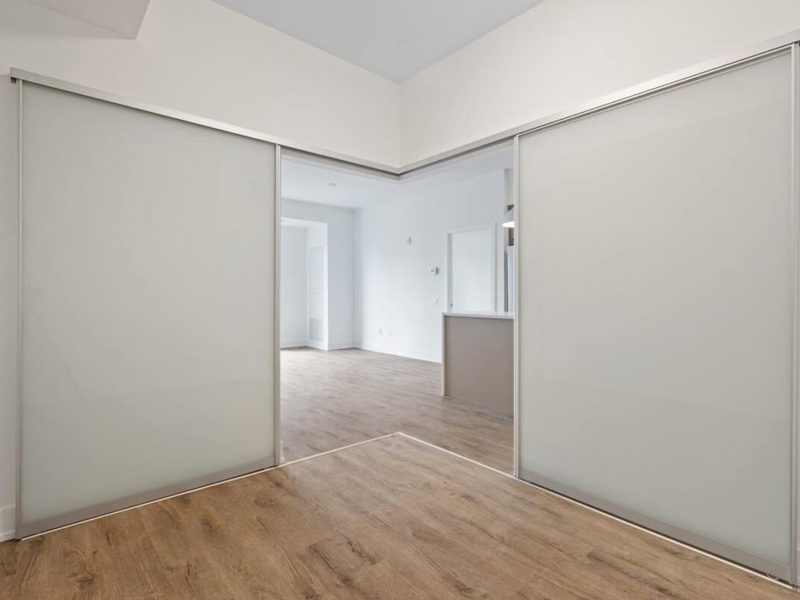
Molding Technology
Extrusion Molding
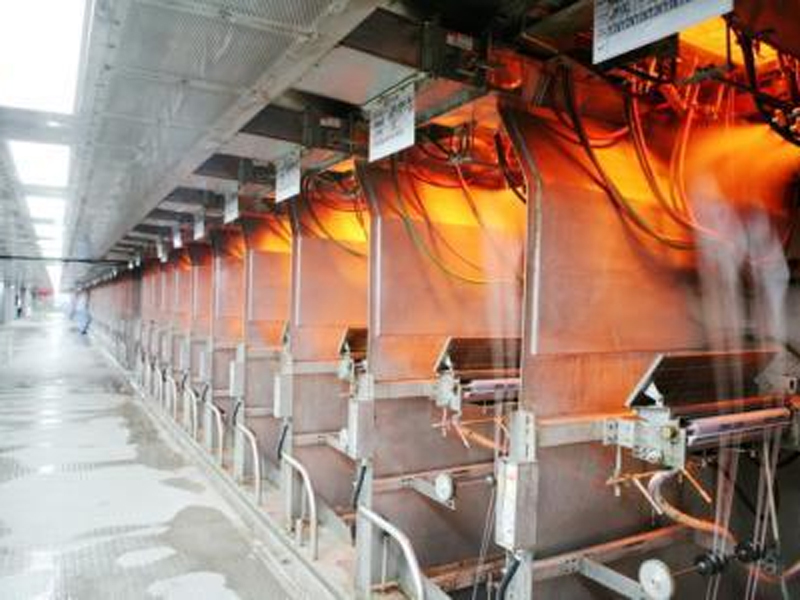
Injection Molding
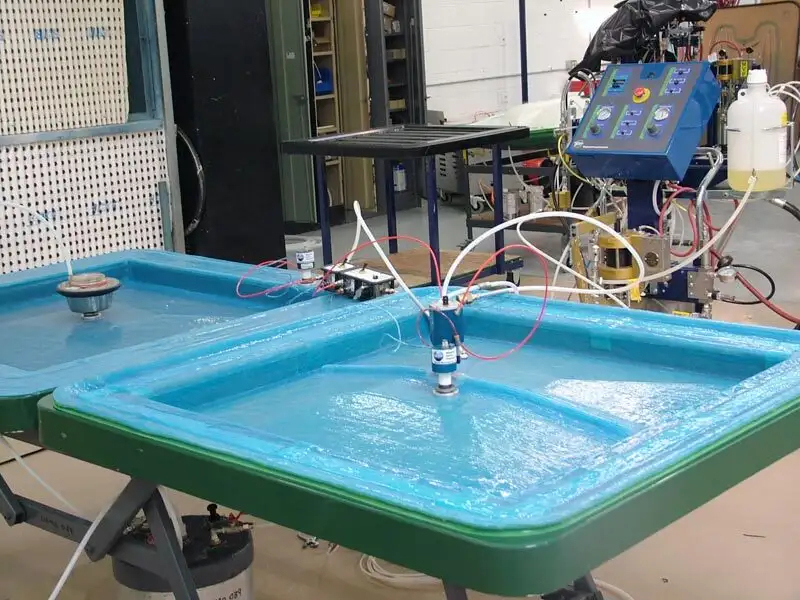