A direct roving for filament winding is one of the most crucial components in the filament winding process. Filament winding, also known as fiber winding, is a technique used to manufacture composite structures for various applications, including aerospace, automotive, construction, and sports equipment.
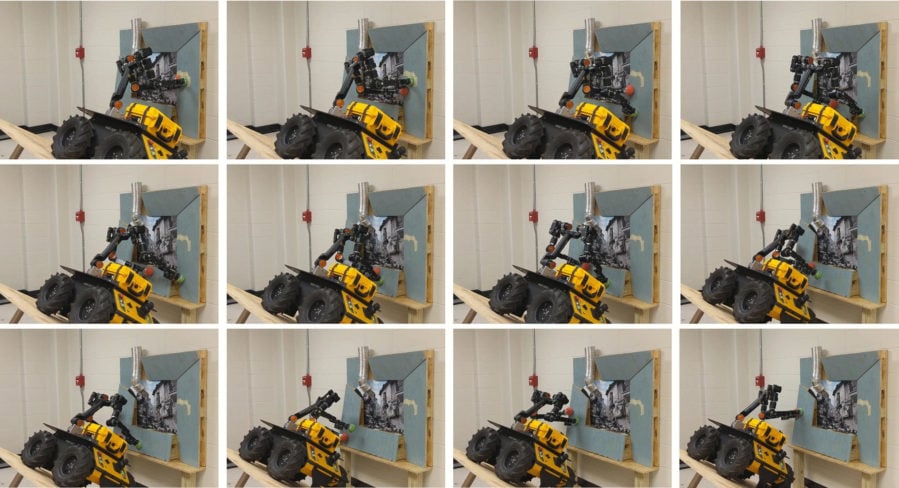
The technique involves winding continuous fibers, such as carbon, glass, or aramid, onto a rotating mandrel in a specific pattern. The fibers are impregnated with a resin matrix, such as epoxy, polyester, or vinyl ester, to form a composite material with desirable mechanical properties.
Direct roving for filament winding is the primary reinforcement used in the filament winding process. It is a continuous fiber bundle with a high tensile strength and stiffness, designed to withstand the winding tension and provide structural reinforcement to the composite part.
In this blog post, we will explore the features, benefits, and applications of direct roving for filament winding and how it contributes to the performance and quality of the final composite part.
Features of Direct Roving for Filament Winding
Direct roving for filament winding is manufactured using high-quality E-glass or S-glass fibers with a continuous filament diameter ranging from 9 to 13 micrometers. The roving is designed to provide excellent mechanical properties, such as high tensile strength, modulus, and fatigue resistance.
The roving is coated with a sizing formulation, which improves its adhesion to the resin matrix during the winding process. The sizing also enhances the roving's compatibility with different resin systems, such as epoxy, polyester, or vinyl ester.
Direct roving for filament winding is available in different tex sizes, ranging from 450 tex to 2400 tex, to meet various application requirements. The roving can also be customized to provide specific properties, such as electrical conductivity, thermal stability, or corrosion resistance.
Benefits of Direct Roving for Filament Winding
Direct roving for filament winding offers several benefits to the composite manufacturer. Here are some of the key advantages of using direct roving for filament winding:
1. High mechanical properties: Direct roving for filament winding provides high tensile strength and stiffness, which makes it an ideal reinforcement for structural composite parts that require high load-bearing capacity.
2. Good processability: Direct roving for filament winding has an excellent winding uniformity, which ensures consistent fiber placement and resin impregnation. The roving has low fuzz and static charge, which reduces processing defects and enhances the quality of the final part.
3. Cost-effective: Direct roving for filament winding is a cost-effective solution for manufacturing composite parts, as it offers a high fiber-to-resin ratio and can be customized to meet specific performance requirements.
4. Versatile: Direct roving for filament winding can be used to manufacture a wide range of composite parts, such as pipes, pressure vessels, wind turbine blades, and sporting goods.
Applications of Direct Roving for Filament Winding
Direct roving for filament winding is used in various applications that require high-performance composite parts. Here are some of the key industries and applications that use direct roving for filament winding:
1. Aerospace: Direct roving for filament winding is used to manufacture composite parts for aircraft and spacecraft, such as structural components, engine nacelles, and fuel tanks.
2. Automotive: Direct roving for filament winding is used to manufacture composite parts for cars and trucks, such as chassis components, body panels, and suspension systems.
3. Energy: Direct roving for filament winding is used to manufacture composite parts for renewable energy systems, such as wind turbine blades, hydroelectric generators, and solar panel frames.
4. Sporting goods: Direct roving for filament winding is used to manufacture high-performance sporting goods, such as tennis rackets, golf clubs, and fishing rods.
Conclusion
Direct roving for filament winding is a critical component in the filament winding process, as it provides structural reinforcement and enhances the performance of the final composite part. The roving offers several benefits, such as high mechanical properties, processability, cost-effectiveness, and versatility, which make it an ideal choice for manufacturing various composite parts.
If you want to learn more about direct roving for filament winding or need assistance in selecting the right roving for your application, contact a reliable manufacturer or supplier who can provide you with the necessary technical support and resources.