When it comes to producing high-quality industrial components such as pipes and tanks, centrifugal casting is an effective technique that has proven to be reliable time and time again. One of the most important aspects of centrifugal casting is the quality of the rovings used in the process. In this blog, we will discuss the various reasons why glassfiber/'>glassfiber roving for centrifugal casting is the perfect choice for your industrial needs.
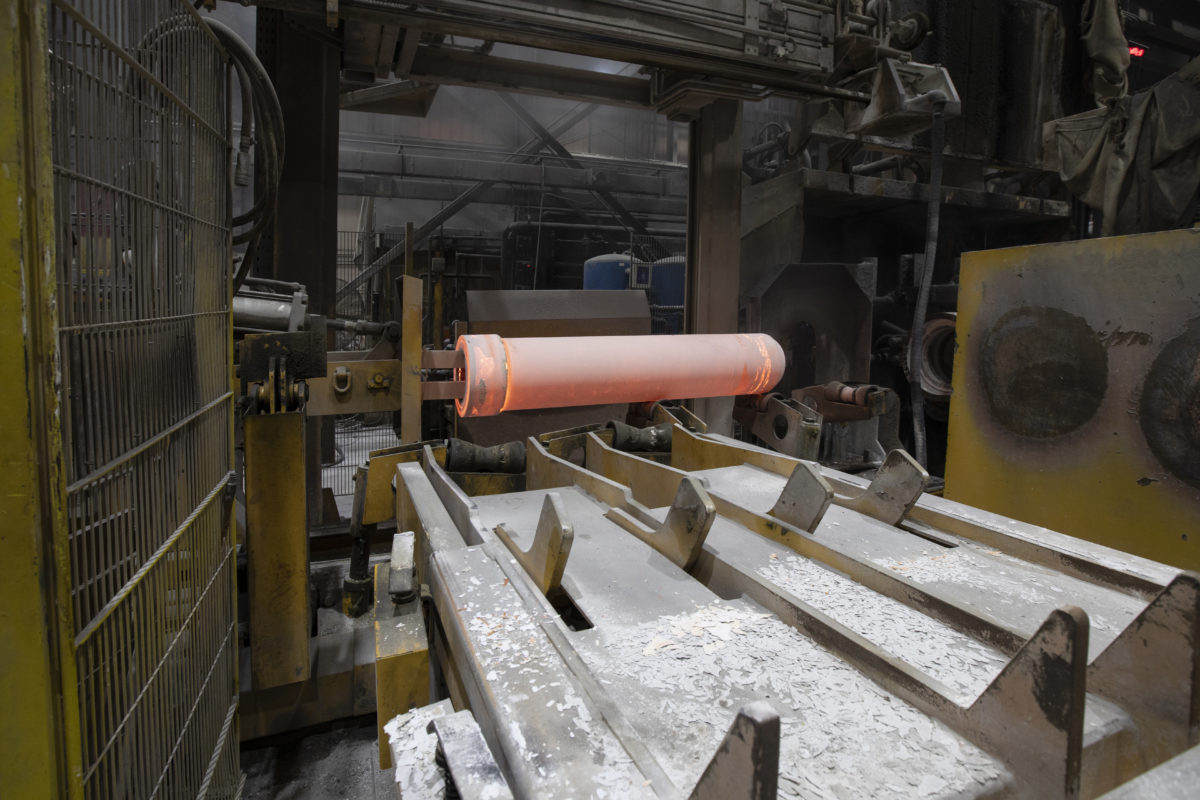
What is centrifugal casting?
Before diving into why glassfiber roving is the ideal choice, let's understand what centrifugal casting means. Centrifugal casting is a process used for the manufacture of hollow cylindrical components. The process involves the pouring of molten material into a rotating mold, and the centrifugal forces generated during the rotation help to evenly distribute the material in the mold. This results in a high-quality surface finish and a uniform thickness throughout the component.
Now, let's move onto why glassfiber roving is the best choice of material for use in centrifugal casting.
Glassfiber roving for centrifugal casting: The benefits
1. High strength-to-weight ratio
One of the most significant advantages of glassfiber roving is its excellent strength-to-weight ratio. The high-strength fibers provide a degree of reinforcement that is unmatched by other materials. This results in components that have excellent mechanical properties, making them suitable for use in a wide range of applications.
2. Corrosion resistance
Glassfiber roving is highly resistant to corrosion. This is because the glass fibers used in the roving are inert and do not react to chemicals or other elements in the environment. Components made using glassfiber roving last longer and require less maintenance than those made using other materials.
3. Unwinding and chopping properties
Another benefit of glassfiber roving is its unwinding and chopping properties. Rovings that have good unwinding properties can be easily unwound from a package without tangling, while those with good chopping properties can be easily cut to the desired length without creating flyaway strands. This makes the roving highly efficient and easy to work with, reducing production time and costs.
4. Thermal insulation
Glassfiber roving provides excellent thermal insulation properties. This makes it an ideal choice for use in components that require temperature control. Components made using glassfiber roving are able to withstand high temperatures, ensuring that the material does not degrade even under the most extreme heat.
5. Chemical resistance
Glassfiber roving is highly resistant to chemicals, including acids, alkalis, and solvents. This makes it an ideal choice for use in components that are exposed to harsh chemicals, such as pipes and tanks used in the chemical industry. The material is also highly flame resistant, making it safe for use in high-temperature applications.
In conclusion, glassfiber roving is an excellent choice for use in centrifugal casting due to its strength, corrosion resistance, unwinding and chopping properties, thermal insulation, and chemical resistance. Choosing this material for your industrial needs will result in components that are of high quality, durable, and long-lasting. If you're looking for a material that can deliver consistent results, then glassfiber roving is the perfect choice.